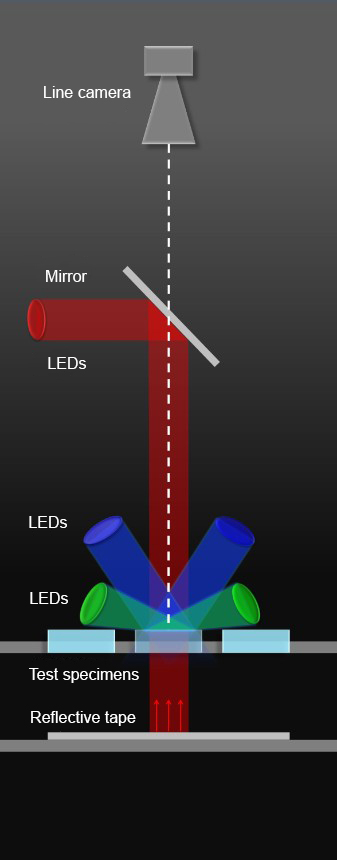
Task and solution
Challenge
One challenge currently facing industrial image processing is the need to detect inclusions
and air bubbles in transparent materials of any shape and form.
Technical properties
- Inspection of transparent objects, including complex shapes
- Differentiation between inclusions of foreign objects and air bubbles
- Material flow speeds up to 3m/s
- Inspection in free fall
- Capable of inspecting objects in the mm² - m²
size range
Solution
The patented Purity system developed by Fraunhofer IOSB identifies and differentiates
between changes in transparency, inclusions of foreign objects and air bubbles – almost
regardless of the object's shape. In contrast to conventional systems,Purity
allows inspection to be performed entirely from a single perspective.
Fields of application
- Application in glass production
- Production of glass tubes and glass rods
- Application in the automotive industry